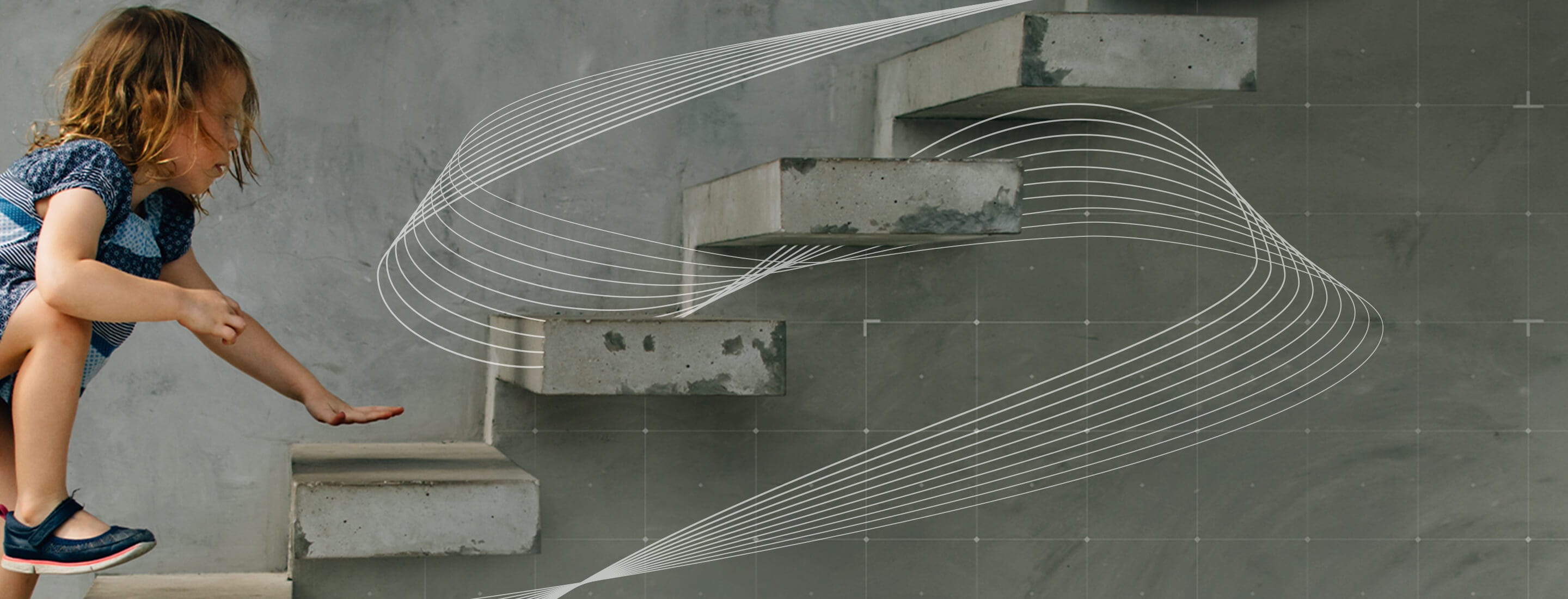
خرسانة أقوى بإعادة تدوير ثاني أكسيد الكربون
بعد الماء؛ تُعد الخرسانة من أكثر المواد التي صنعها الإنسان استخدامًا على وجه الأرض، ففي العام 2022م وحده، تم إنتاج ما يقارب 4,158 مليون طن من الأسمنت، المكون الرئيس للخرسانة، ومع ذلك فإن الأسمنت؛ يُعتبر مسؤولًا عن 7-8% من انبعاثات ثاني أكسيد الكربون في العالم سنويًا.
وفي حين كان التركيز في قطاع الخرسانة عامة مُنصبًّا على التفكير فقط في كيفية تقليل انبعاثات ثاني أكسيد الكربون، فقد يسلط عملنا الضوء على ابتكار طريقة نستخدم فيها ثاني أكسيد الكربون كجزء من عملية المعالجة لتصنيع الخرسانة.
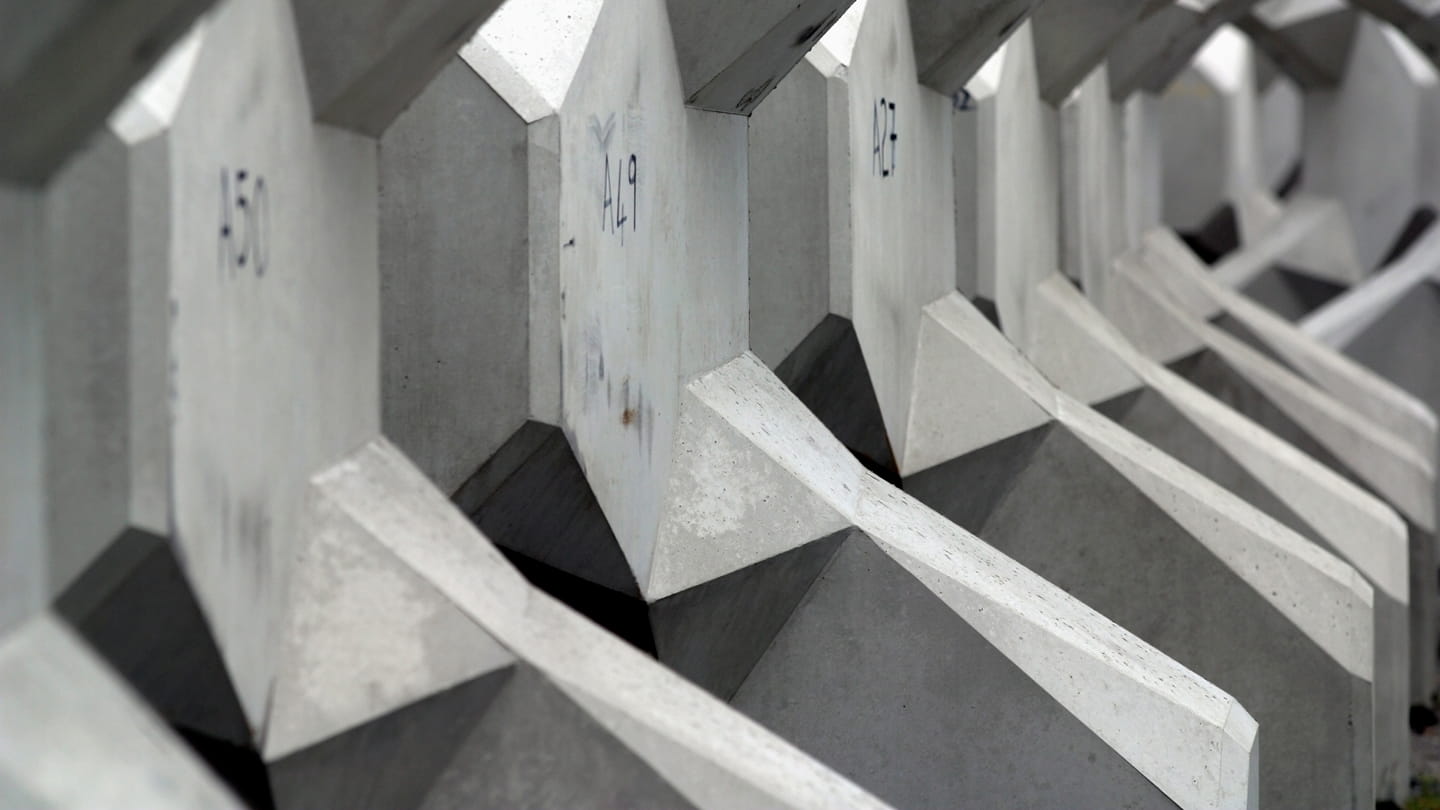
لبِنات أساس لبناءٍ راسخ
بأبسط شكلٍ ممكن؛ يتم دمج الإسمنت والرمل والماء والركام لإنتاج الخرسانة، وعندما يُمزج الإسمنت بالماء، ينتج عن ذلك مجموعة من التفاعلات الكيميائية والتي تسمح للمزيج بأن يصبح صلبًا فيما بعد.
يمكن أن تتأثر هذه العملية بعدة عوامل، كدرجة الحرارة الخارجية أو حتى كمية الإسمنت في الخليط. لكن الأهم هو احتفاظ الخرسانة بالكمية المناسبة من الرطوبة على أن يتم حفظها في الغالب في درجة حرارة مناسبة ولمدة زمنية حتى تصل لأقصى قوة، إذ أن جفافها بسرعة كبيرة يفقدها قوتها وصلابتها، ومن هنا يأتي دور المعالجة.
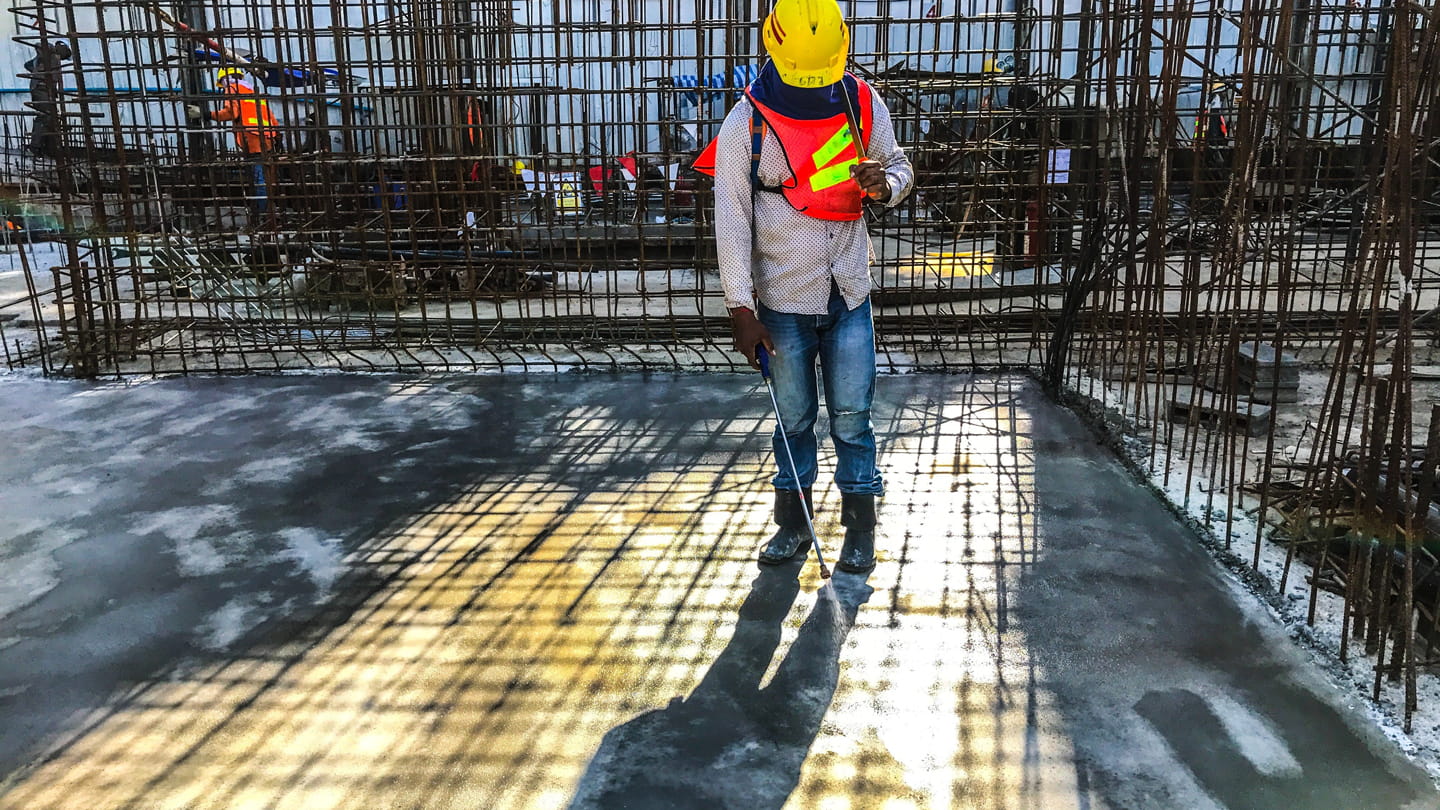
المعالجة الحاسمة
تؤدي عملية المعالجة دروًا مهمًا في إنتاج الخرسانة حيث تساعد على حمايتها من فقدان الرطوبة، ولا تزيد العملية من قوة الخرسانة فحسب، بل تجعلها أيضًا أكثر متانة ومقاومة للتشقق والتصلب والذوبان وتمنحها نفاذية أقل للماء.
توجد العديد من الطرق للمعالجة، من استخدام البخار أو رش السطح برذاذ، أو حتى تغطيته بنسيج أو صفائح بلاستيكية تحفظ الرطوبة، حيثُ أن الفرصة لابتكار جديد كانت سانحة أمامنا لمعالجة الخرسانة الجاهزة باستخدام انبعاثات ثاني أكسيد الكربون.
قصة نجاح يكتبها الجميع
يمكن لتقنيات استخلاص الكربون مثل تقنية استخلاص انبعاثات الكربون من الوسائط المتحركة واحتجازه في المنشآت الصناعية أن تقلل الانبعاثات الناتجة من هذه المنشآت، وبالتالي منع وصولها إلى الغلاف الجوي، لكن يبقى السؤال، ماذا يمكننا أن نفعل بثاني أكسيد الكربون الذي قمنا باحتجازه؟
تشمل الخيارات المُتاحة احتجاز الكربون في باطن الأرض أو إعادة تدويره.
حيثُ أن إعادة استخدام الكربون تعد واحدة من أربعة طرق تشمل الحدّ والإزالة وإعادة التدوير، مما يُسهم في تعزيز الاقتصاد الدائري منخفض الكربون، وكل هذا نابعٌ من إيماننا بأن فكرة مثل هذه كفيلة بالإسهام في تقليل الانبعاثات العالمية مع ضمان نموٍ اقتصاديٍ ثابت، وما ابتكاراتنا في هذا الصدد إلا دليل عملي على ذلك.
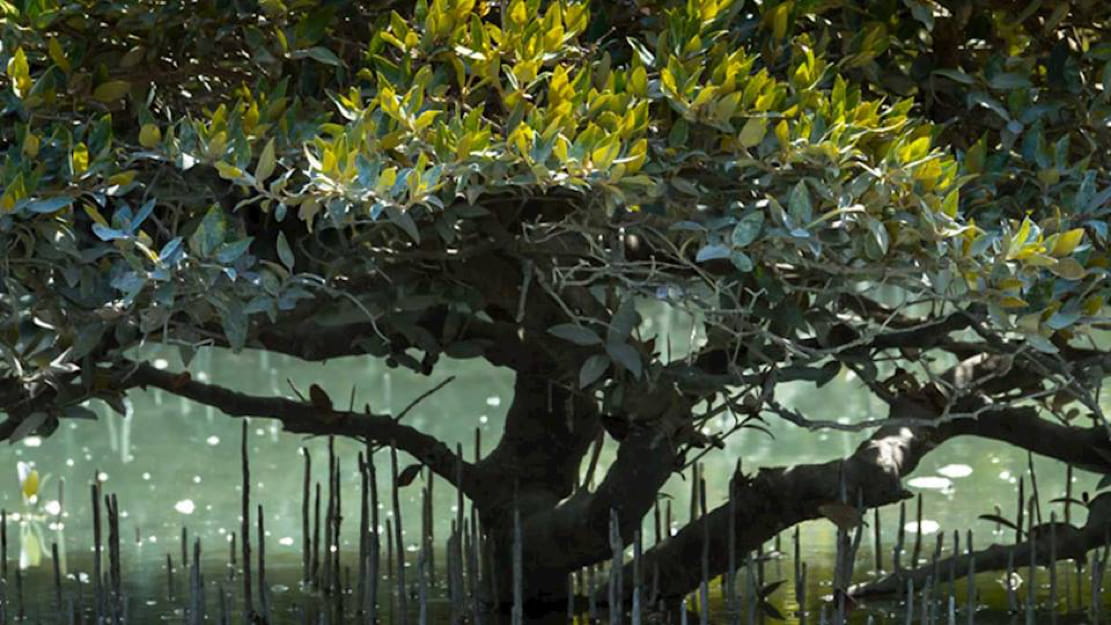
من مجرد فكرة إلى واقع ملموس
بدأنا مشروعنا البحثي في عام 2014م، حيثُ عملنا بالتعاون مع المعهد الكوري المتقدم للعلوم والتقنية على دراسة إمكانية استخدام ثاني أكسيد الكربون في عملية معالجة الخرسانة. ثم قمنا بالتعاون مع شركة محلية للخرسانة الجاهزة للتأكد من الوقت والكيفية اللتين يمكننا من خلالهما استخدام تقنيات استخلاص الكربون واحتجازه.
كانت الفكرة تكمن في إنشاء حوض لاحتجاز الكربون داخل الخرسانة، دون الإضرار أو حتى التأثير سلبًا على جودة وصلابة المنتج النهائي، ولتحقيق ذلك اختبرنا تركيبات وتركيزات مختلفة لثاني أكسيد الكربون، وكان مفتاح نجاحنا يرتكز على الجمع بين ثاني أكسيد الكربون والبخار في آنٍ واحد لتكون النتيجة احتجاز نسبة 20% من ثاني أكسيد الكربون في الإسمنت داخل الخرسانة.
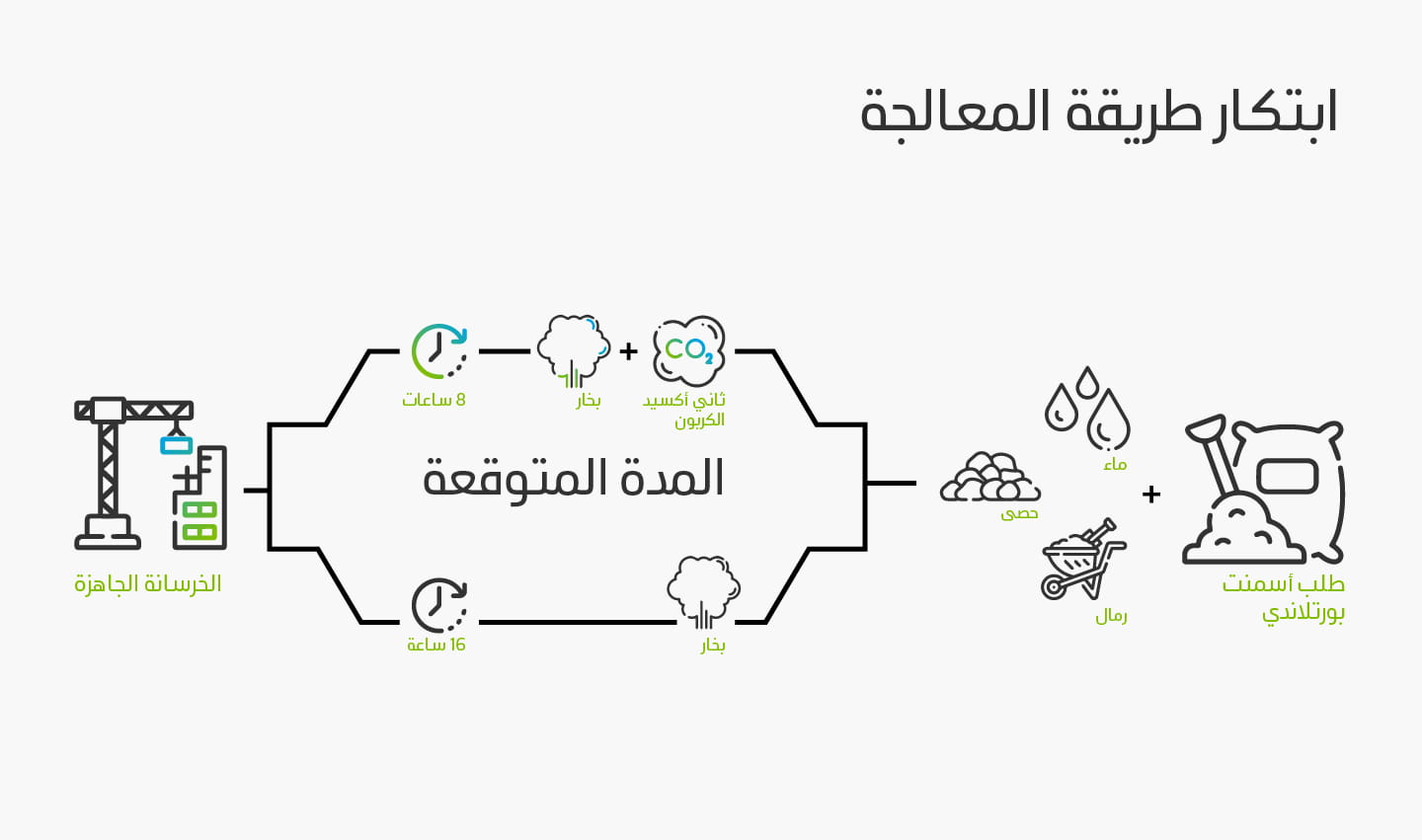
خرسانة أقوى.. بإنتاج أسرع
بعدما تكللت نتائجنا المخبرية بالنجاح؛ قمنا باستخدام تقنياتنا محليًا في معمل محلي للخرسانة مسبقة التصنيع.
كان الاختبار الأهم والذي يجب أن تجتازه الخرسانة المعالجة بالكربون هو قياس قوتها الميكانيكية، حيث كان معيار صناعة الخرسانة المستخدمة هو 35 ميغا باسكال، وإذا فشلت مجموعة من الخرسانة في الوصول إلى هذا الرقم تحديدًا خلال 28 يومًا، فسيتم رفضها تمامًا.
كانت النتائج مذهلة، فتقنياتنا لم تتجاوز المعايير في يوم واحد فحسب، بل قللت كذلك المدة المستغرقة في فصل الخرسانة من الحوض إلى النصف، الأمر الذي بالعادة يستغرق 16 ساعة.
والأهم من ذلك، أن الخرسانة المعالجة أكثر متانة من الخرسانة التقليدية، مما أدى إلى انخفاض نفاذية الماء مع مقاومة أكبر للكلور والكبريتات، والتي تعد لبنةً أساس للبناء في المناطق البحرية أو الأماكن ذات الرطوبة العالية.
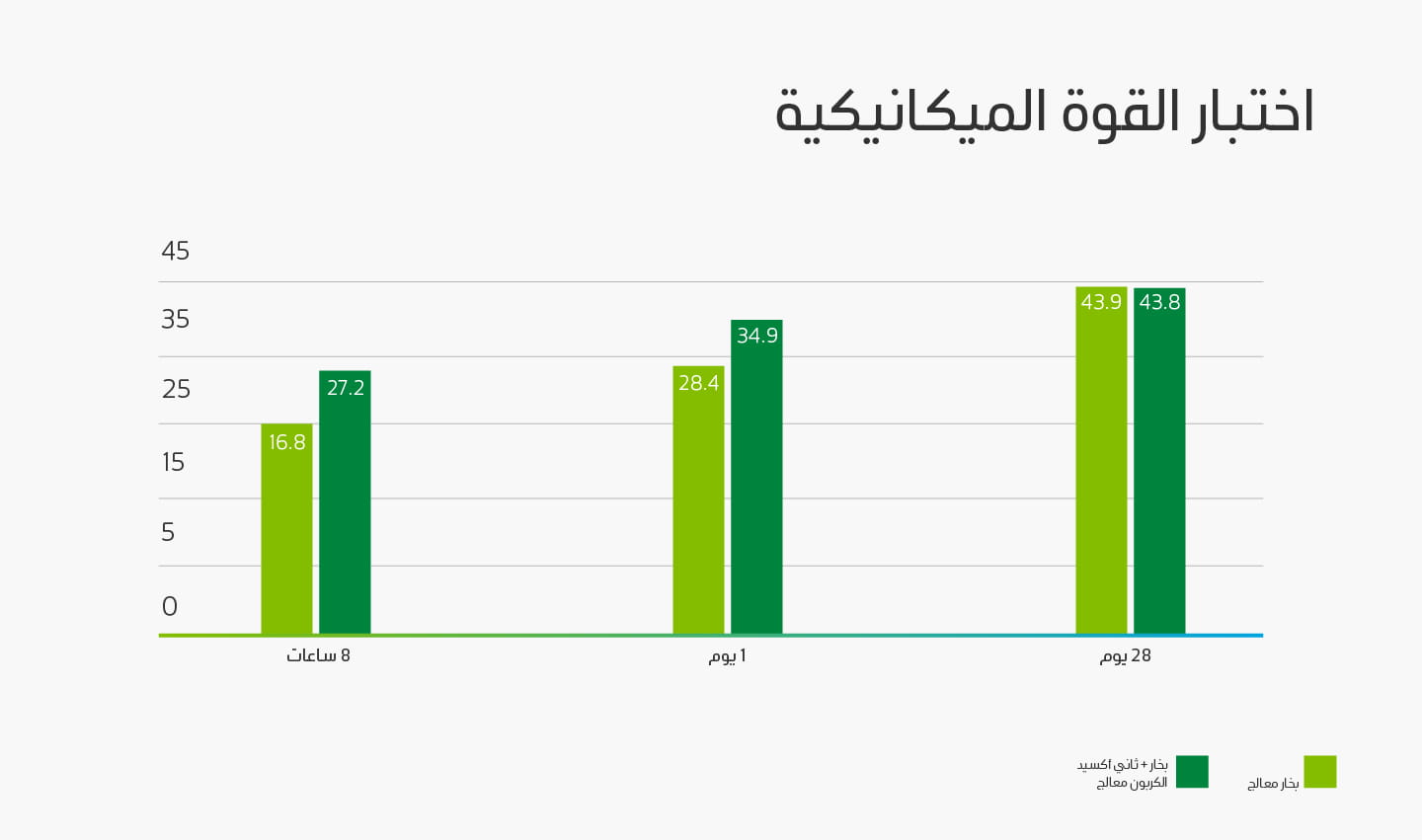
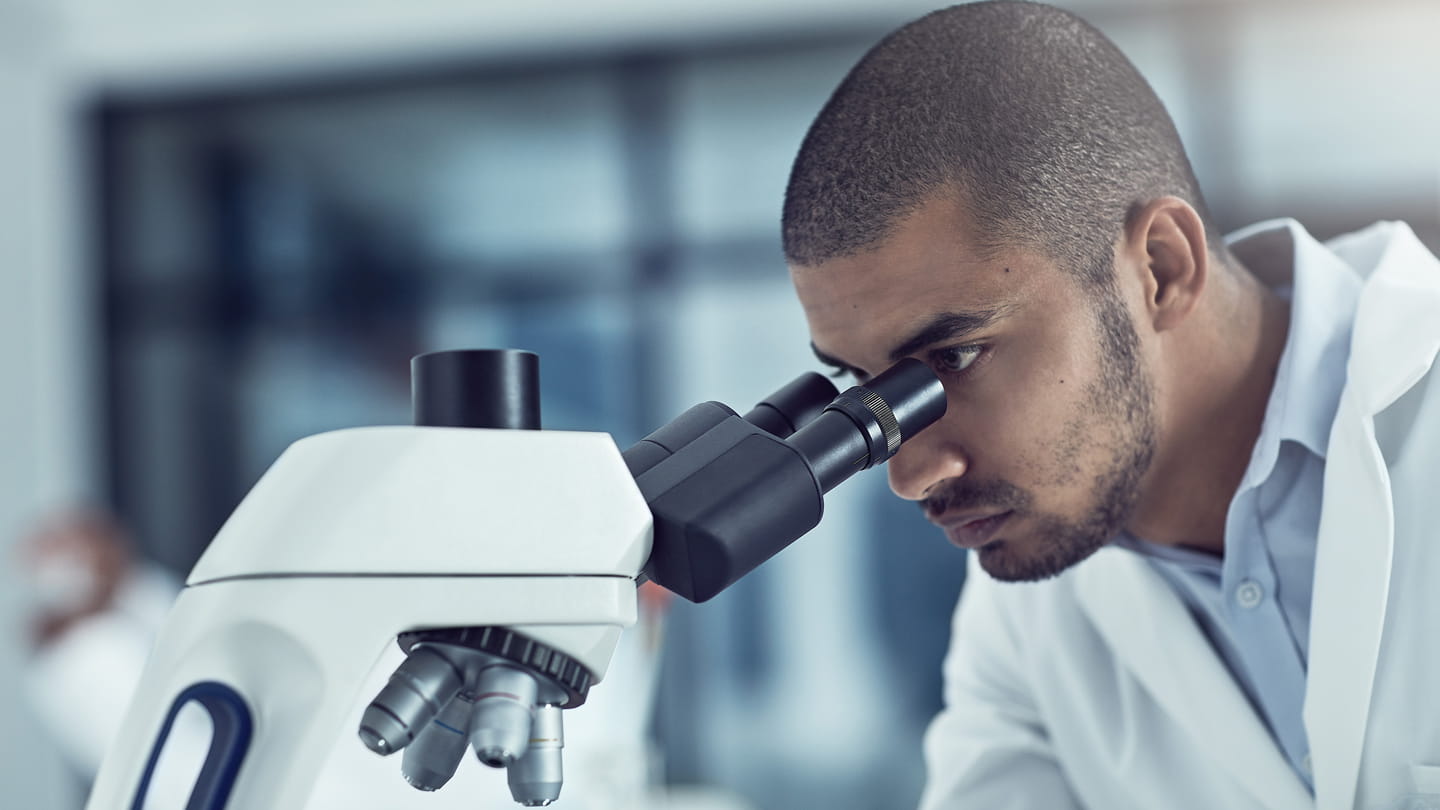
بناءٌ للمستقبل
بعد النجاح الذي حققناه في احتجاز 20% من ثاني أكسيد الكربون، فإن الإمكانات التي تتمتع بها هذه التقنية هائلة، خاصةً بعد أن يتم استخدامها تجاريًا.
وبالتالي، إذا تم تطبيق ابتكارنا في المعالجة بالكربون في قطاع الخرسانة عالميًا، فيمكننا إعادة تدوير ما يصل إلى 246 مليون طن من ثاني أكسيد الكربون سنويًا - أي ما يعادل إزالة الانبعاثات من 53 مليون سيارة. أما هدفنا التالي فهو اختبار تقنيتنا المبتكرة في عملية إنتاج الطوب وخليط الخرسانة الجاهز.
ويبقى السؤال: ماذا لو اُستخدم ثاني أكسيد الكربون المنبعث من عملية إنتاج الإسمنت نفسها؟ عندها سيكون قطاع الخرسانة قادر على تقليل تأثيره البيئي ككل، من أجل مستقبلٍ أقل انبعاثًا وأكثر نقاءً.
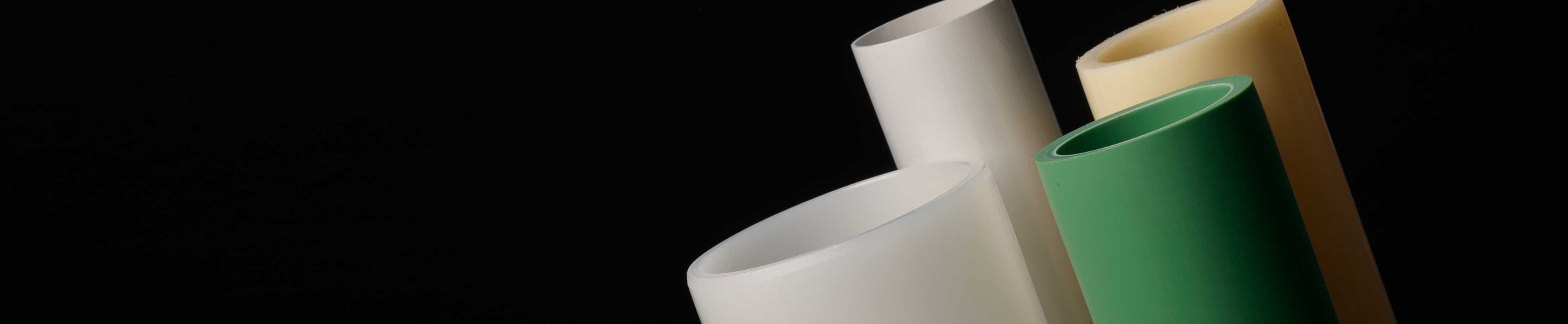