
Carbon curing
After water, concrete is the most widely-used material on earth. Approximately 4,158 million tons of cement — the principle ingredient in concrete — were produced in 2022. However, production of cement is also responsible for around 7-8% of annual global CO2 emissions.
While there is a clear desire to reduce CO2 emissions across the whole concrete industry, we are innovating the way concrete is manufactured to utilize CO2 as part of the curing process.
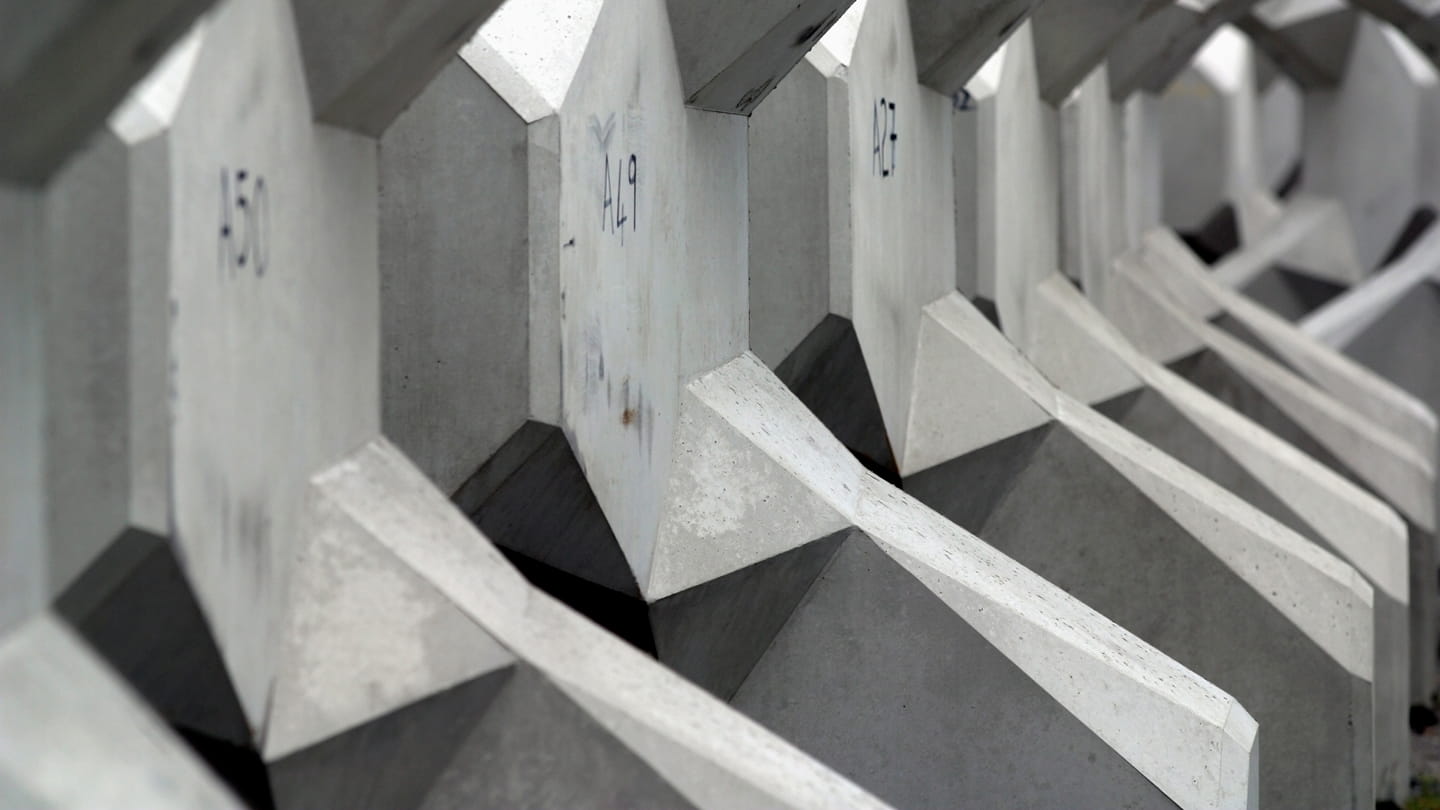
The basic building blocks
In its simplest form, cement is combined with sand, water, and aggregate to produce concrete. When the cement and water are mixed it causes a series of chemical reactions that set and harden the overall mixture.
This process can be affected by a number of factors, from the outside temperature to the amount of cement in the mixture. What is crucial though, is that the concrete retains the right amount of moisture and is kept at the right temperature over a period of time to attain its full strength. If it dries out too quickly, the concrete will be significantly weakened — and that’s where curing comes in.
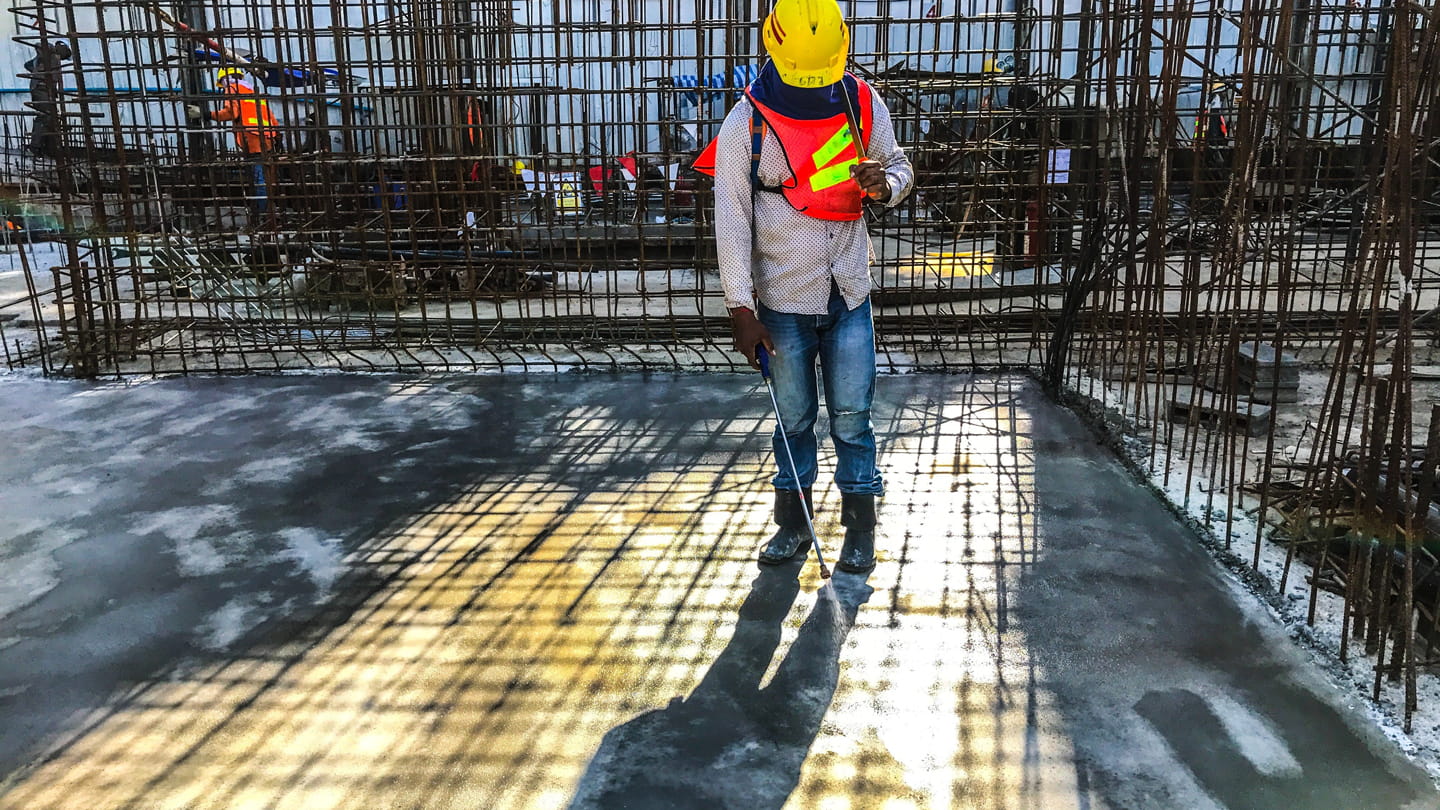
Curing is crucial
Curing is an important process in concrete construction that controls moisture loss. It not only increases the strength of the concrete, it also makes it more durable, less permeable to water, and more resistant to cracking, freezing, and thawing.
There are many different curing methods available, from using steam or spraying the surface with a fog mist, through to covering it with moisture-retaining fabric or plastic sheets to prevent moisture loss. We saw the opportunity to innovate a new way of curing precast concrete using CO2.
A win-win scenario
Technologies like mobile carbon capture and carbon capture at industrial plants can potentially reduce carbon emissions from facilities that employ them, preventing them from reaching the atmosphere. But the question remains, what do you do with all the CO2 you’ve captured?
Options include sequestering it deep underground, or, as in this case, developing a way to recycle it.
Reusing CO2 is one of the four “Rs” (alongside reducing, removing, and recycling), contributing to the circular carbon economy. We believe this idea has the power to reduce global emissions while ensuring consistent economic growth. And our carbon curing innovation is a perfect example of this in action.
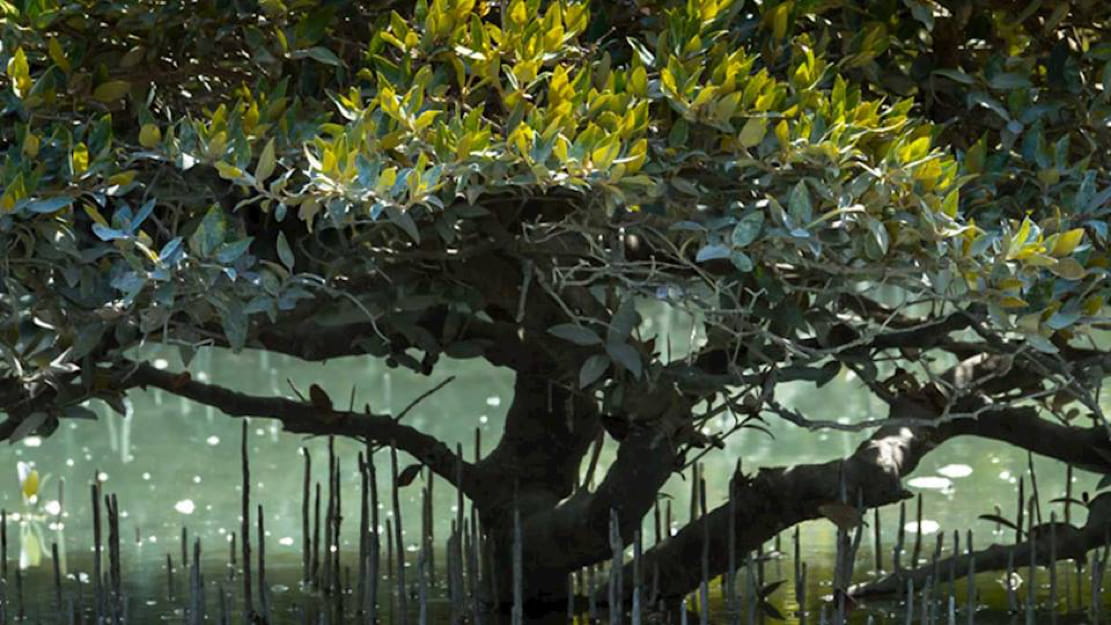
Putting theory into practice
We began our research project in 2014, working alongside the Korea Advanced Institute of Science and Technology (KAIST) to study the potential of using CO2 in the concrete curing process. Then, our next step was to collaborate with a local precast company to ascertain exactly when and where we could introduce the captured CO2.
Our idea was to create a 'sink' for CO2 within the concrete, without harming or negatively effecting the strength of the end product. To achieve this, we tested different curing combinations and CO2 concentrations. The key was combining CO2 and steam — resulting in an impressive 20% CO2 uptake in the cement within the concrete.
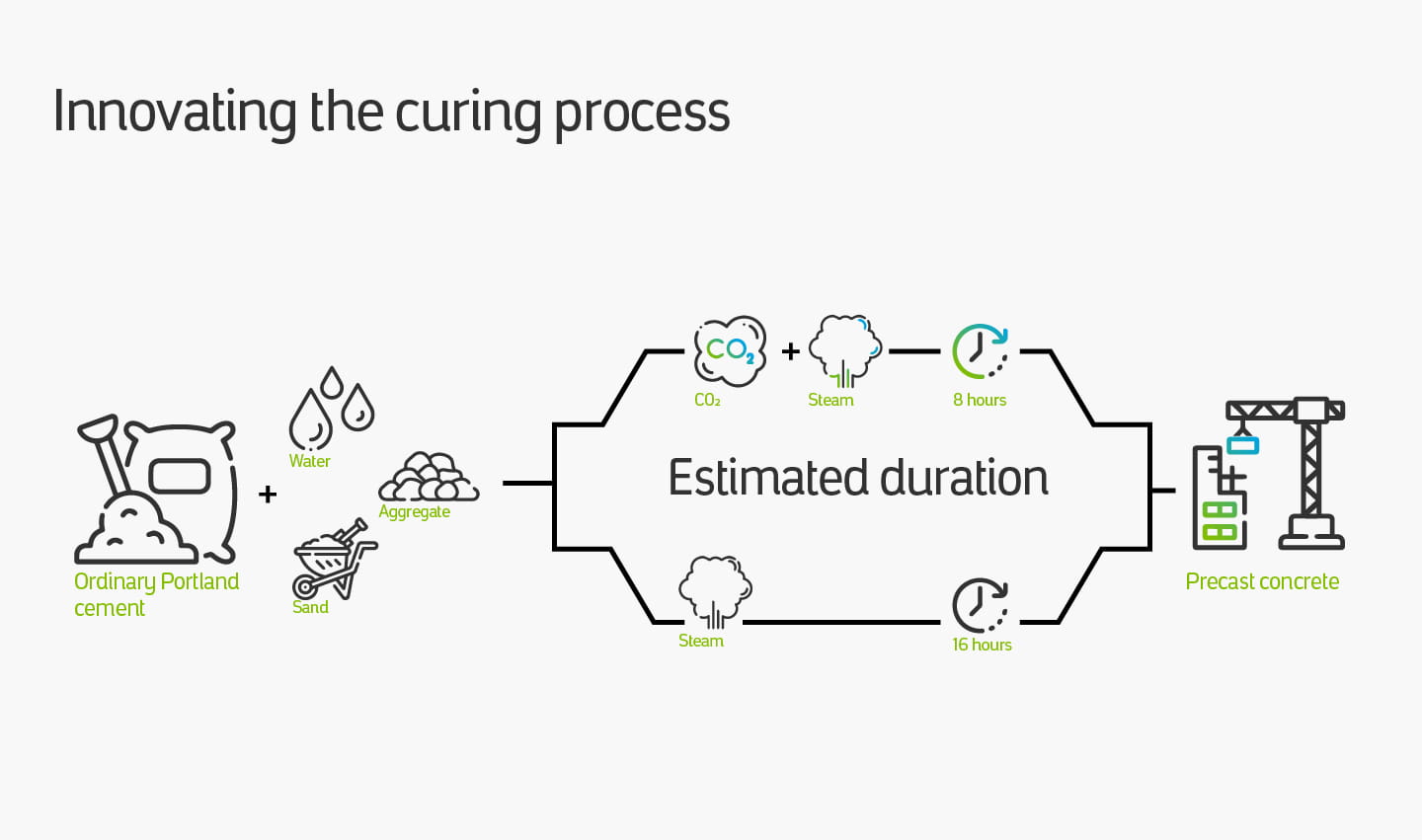
Stronger concrete, produced faster
Following our successful lab test, we put our technology to work locally, in a local precast concrete plant.
The most important test that our carbon-cured concrete had to pass was measuring its mechanical strength. The industry standard for the precast concrete we selected is 35 megapascals (MPa), and if a batch of concrete fails to reach it in 28 days, it will be rejected completely.
Not only did our technology reach the benchmark in just one day, but it also helped reduce the time it takes to remove concrete from molds — around 16 hours — by half.
And what’s more, our concrete was also more durable than traditional concrete, showing lower water permeability and greater chlorine and sulfate resistance, all of which are crucial in construction offshore or in places with high humidity.
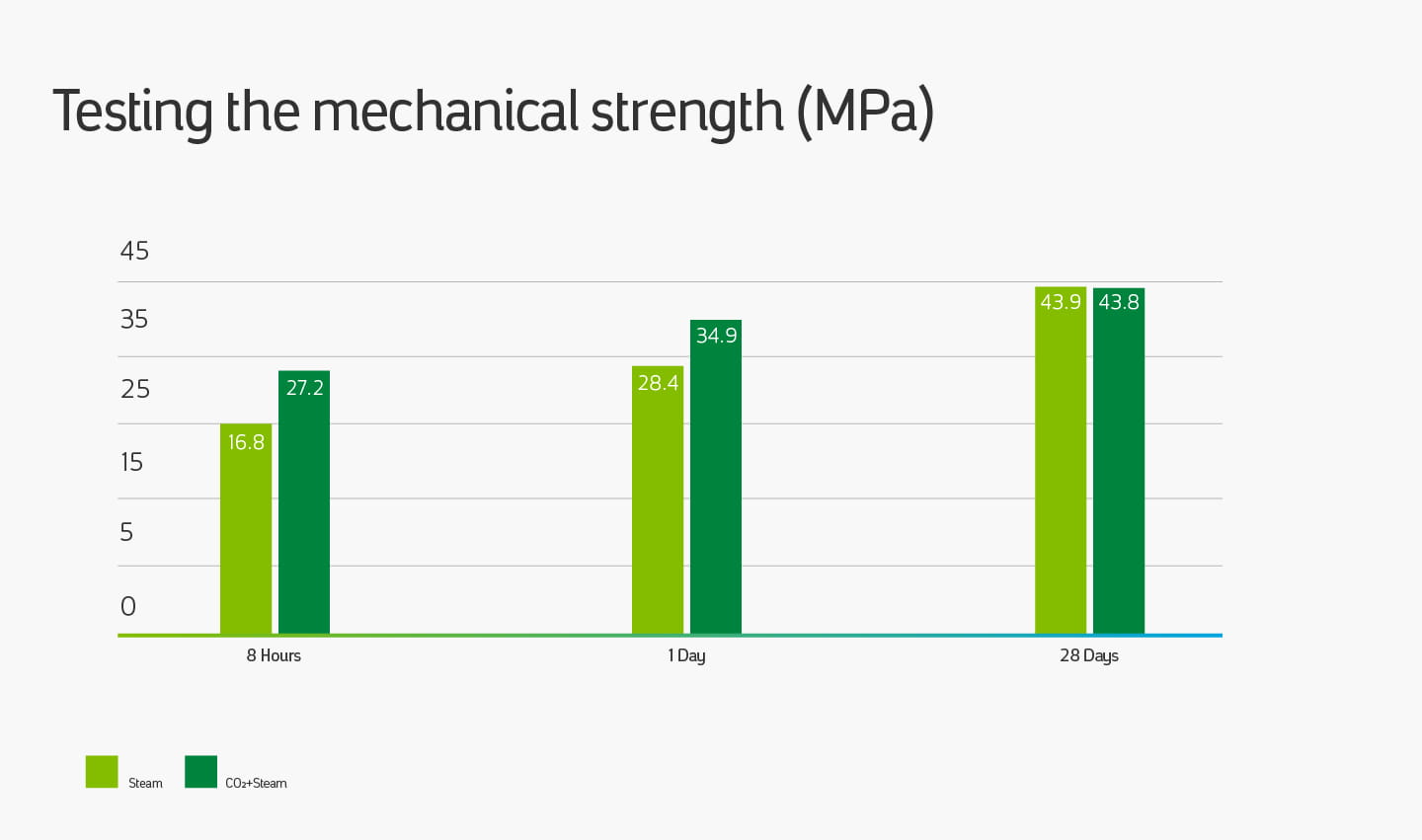
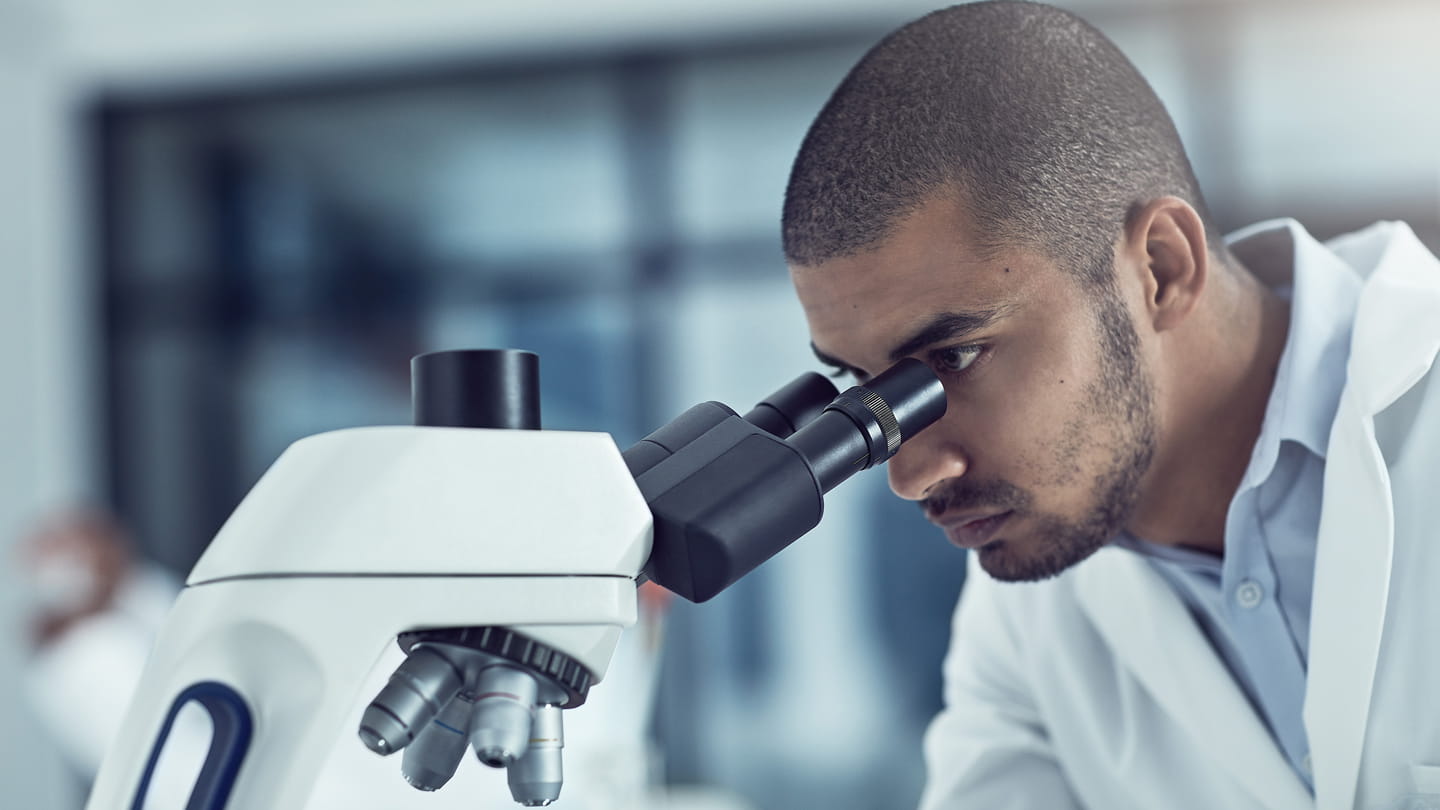
Building for the future
Having achieved 20% CO2 uptake, the potential for our technology is huge once it is commercialized.
In fact, if the global precast concrete industry switched to our carbon curing innovation, it could recycle up to 246 million tons of CO2 a year — equivalent to removing emissions from 53 million cars. Our next goal is to test our carbon curing technology in the production of bricks and ready-mix concrete.
Imagine if the CO2 created by the cement production process itself was reused? Then the industry as a whole would be able to reduce its environmental impact, and transition to a lower-carbon future.
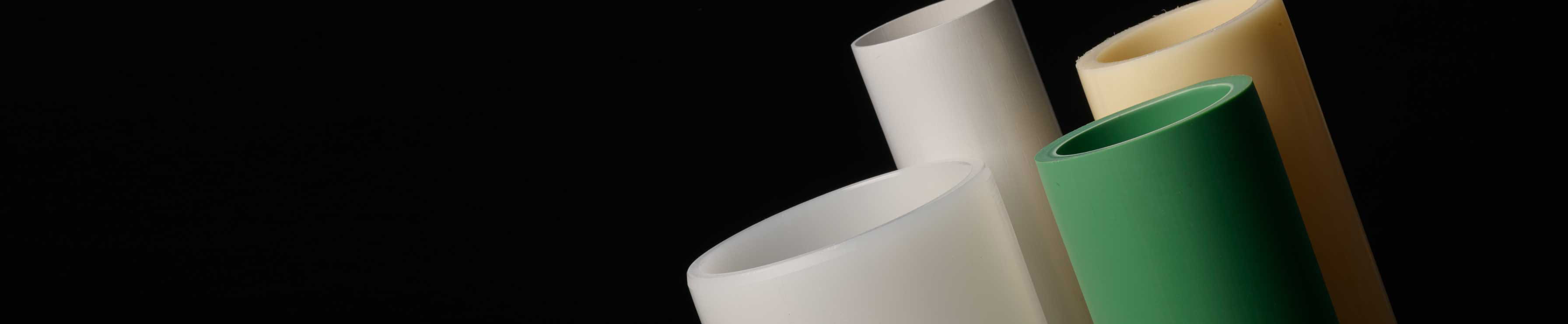